Turning the Page on Rework: How Goldbeck Uses AR for Superior Results
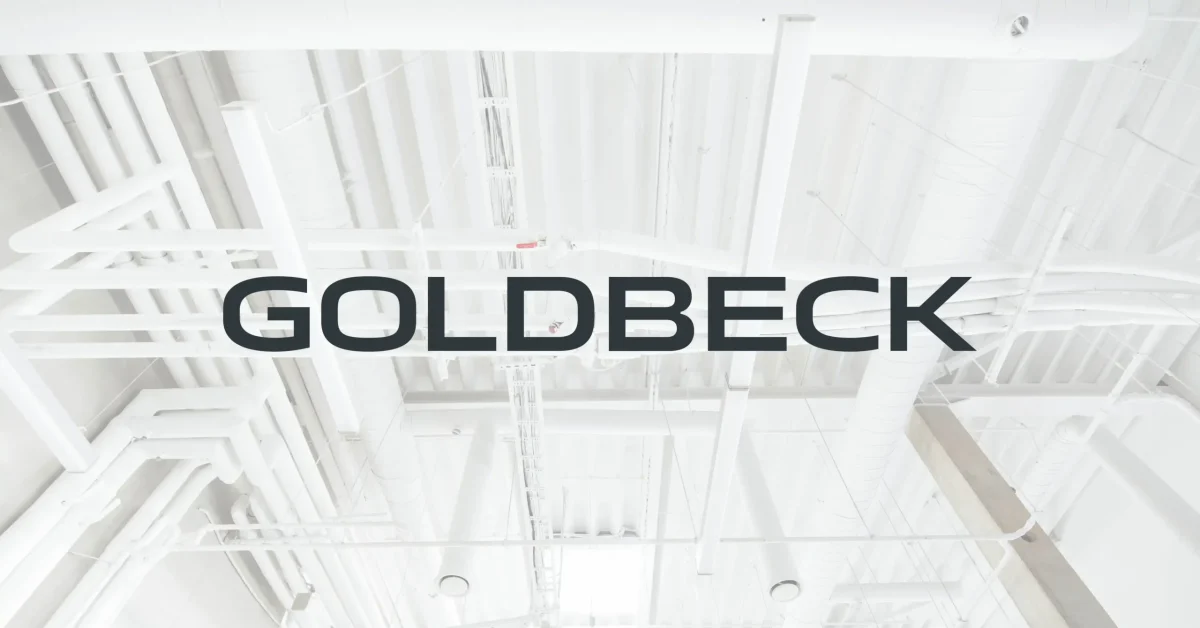
Table of Contents
Share this post
As long as there’s been construction, there has been rework.
A 2022 white paper by Autodesk and FMI revealed that, just in the U.S. alone, $65 billion is being lost each year to rework.
Poor communication, design errors, and late clash detection can all trigger massive delays, soaring budgets, and strained relationships between stakeholders.
Large-scale projects feel this impact even more.
Research from McKinsey showed that 98% of megaprojects experience cost overruns exceeding 30%, while 77% get delivered at least 40% behind schedule.
Goldbeck GmbH, one of Germany’s leading construction firms, faced these challenges head-on and found a solution that redefined their approach—GAMMA AR.
This case study explores how Goldbeck, with over 12,000 employees and €5.2 billion in revenue, leveraged GAMMA AR’s augmented reality solution to cut rework, save costs, and significantly optimize their quality assurance and control (QA/QC) processes along the way.
Communication Breakdowns and Costly Design Misinterpretation
A recent study highlighted that up to 48% of all rework is caused by miscommunication together with low-quality project data, with 26% of rework directly linked to communication failures between team members.
Goldbeck, even with its systematized and modular approach to construction, has also focused on overcoming these issues.
Their projects, spanning industrial buildings, offices, and warehouses, often faced challenges in making sure that on-site teams execute the planned designs as intended.
One of Goldbeck’s key concerns was the difficulty in pinpointing clashes between design plans and jobsite realities early enough to prevent significant rework.
Goldbeck leadership recognized the impacts these events had on their projects, finances, and timelines.
As construction projects grew more complex, 2D plans were no longer sufficient to meet modern demands.
Goldbeck searched for a solution to bridge the communication gap and eliminate errors before they had a chance to escalate.
The Financial and Reputational Impacts of Rework
These communication issues and misinterpretations weren’t just a question of finances for Goldbeck—they also impacted project delivery milestones and overall quality.
Poorly executed designs or late clash detection meant costly rework, additional man-hours, and overextended schedules.
A study by PlanRadar for Europe and the UK showed that rework there can account for as much as 11% of overall construction project costs.
In Goldbeck’s case, these issues meant they were losing valuable time, resources, and risking reputational damage.
Traditional methods like paper plans and manual QA/QC processes couldn’t always keep up with the demands of modern construction, making the need for an innovative solution even more urgent.
Goldbeck's AR-Driven Approach to Solving Construction Challenges
To overcome these challenges, Goldbeck turned to GAMMA AR, an augmented reality (AR) platform that integrates directly into construction workflows, overlaying 3D CAD and BIM models onto the real world.
Goldbeck implemented GAMMA AR across six pilot projects, using it for QA/QC processes, walkdowns, and clash detection.
The platform runs on everyday mobile devices like smartphones and tablets, allowing superintendents and foremen to easily access and use AR on-site without needing heavy investment or specialized training in new hardware.
The results were clear from the start.
Goldbeck reported 360-degree integration with their existing processes, with teams adopting the technology quickly.
By overlaying their design models on-site, in the exact places where they’re being built, GAMMA AR allowed teams to ensure alignment between design intent and actual construction, identifying any possible deviations early on.
Unprecedented Efficiency Gains and Cost Savings
The numbers speak for themselves. With GAMMA AR, Goldbeck reduced their QA/QC time by 80%.
Site teams, who previously spent significant time manually going over plans and verifying work, now had an intuitive AR tool to help them streamline these processes.
As a result, they saved $1,500 per week per job site, totaling an impressive on average $135,000 in weekly savings across 90 job sites.
Pablo Thiemig, an MEP superintendent at Goldbeck, emphasized the time savings and ease of use: “It’s nicer to take five minutes to visualize something with AR than to spend two hours looking at plans.”
This sentiment was echoed by other team members, who reported fewer clashes and a smoother process for addressing any deviations.
Annika Kirsch, Goldbeck’s Product Owner, described GAMMA AR as a game-changer: “Our collaboration with GAMMA AR has streamlined our construction sites and revolutionized our approach to quality control and efficiency. The impact is undeniable.”
Early Clash Detection: A Game-Changer for Construction
Goldbeck’s experience highlights how AR technology can transform the industry’s approach to quality control and communication.
Traditional 2D plans and manual methods simply can’t keep up with the complexity of modern projects.
By integrating AR and BIM models, firms can avoid the common pitfalls of misinterpretation and late clash detection.
One of the key insights from Goldbeck’s use of GAMMA AR is the importance of detecting deviations early.
As Christopher Wright, another Goldbeck superintendent, noted: “The greatest potential of AR is elimination of clashes in advance. If no clash occurs, there’s no need for rework: no man-hours, no additional materials, no extra costs, no problems with the client.”
What’s more, the intuitive nature of GAMMA AR allowed teams to overcome language barriers and improve communication with subcontractors.
Visualizing design intent in real-time meant that issues could be addressed at once, even in cases where language differences might have caused delays.
A New Standard for Quality Control and Cost Savings with AR
Goldbeck’s implementation of GAMMA AR has advanced their construction processes, leading to better communication, faster decision-making, and a dramatic reduction in rework.
By overlaying 3D models directly onto real-world environments, the technology has empowered their teams to detect potential issues much sooner and ensure design precision on-site.
Building on this success, Goldbeck plans to roll out GAMMA AR across more of their projects, further strengthening their leadership in construction efficiency and quality control.
Their experience demonstrates that AR technology is no longer simply for the future—it’s a powerful tool that delivers measurable benefits today.
Ready to Achieve More with GAMMA AR?
If your company is looking to reduce rework, save time, and improve project outcomes, now is the time to see how GAMMA AR can help you achieve these goals.
Discover how GAMMA AR can streamline your construction projects and eliminate costly rework—download a free trial today from the App Store or Google Play.
For a personalized demo and to learn how AR can improve your team’s performance, contact us today and start building smarter.