Before the Wall Closes: How AR is Raising the Bar in Pharma Construction
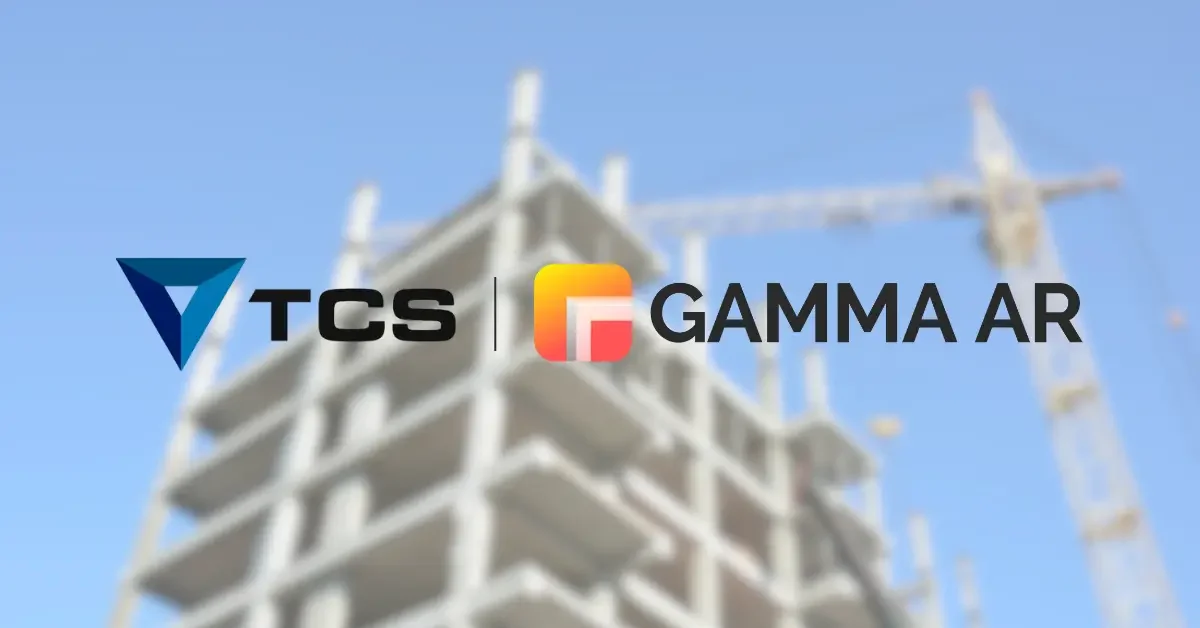
Table of Contents
Share this post
Problem: In pharmaceutical facility construction, even small errors—like a misplaced pipe or a misaligned vent—can lead to significant delays, regulatory non-compliance, and escalating costs.
Impacts: Even small errors can trigger serious delays, financial losses, and compliance risks, with rework and failed inspections compounding challenges in these complex, high-stakes projects.
Solution: Triad Consulting Solutions used GAMMA AR to overlay BIM models on-site, enabling real-time issue detection and alignment before critical phases.
Results: Reduced rework by over 50%, ensuring alignment and compliance before walls and ceilings were closed. Enhanced collaborationbetween field and office teams through on-site issue tracking and visualization. Improved stakeholder engagement by enabling on-site 3D visualizations for faster decision-making and better project alignment.
One mistake. That’s all it takes.
In pharmaceutical facility construction, a misplaced pipe or a misaligned vent not caught right away could mean weeks, if not months, of delays, non-compliance, and spiraling costs.
Teams scramble. Walls get torn down. Timelines disintegrate. Budgets bleed.
But what if there’s a way to catch these errors before they have a chance to wreak havoc?
What if costly rework could be avoided altogether?
In pharma construction projects—where the margin for error is razor-thin—GAMMA AR makes all the difference.
Strict regulatory compliance and the complexity of MEP systems mean even the smallest mistakes can trigger significant delays, rework, and financial loss.
That’s why the construction industry is increasingly seeking innovative solutions like augmented reality to overcome these challenges.
In this article, we’ll look at how Triad Consulting Solutions (Athens, Georgia, US), a leader in pharmaceutical project management, used GAMMA AR to prevent costly rework and ensure regulatory compliance during the construction of a pharmaceutical facility.
GAMMA AR was introduced later in the project yet still played a crucial role in ensuring precision and compliance during critical phases.
Its real-time overlay of the BIM model onto the physical site allowed workers to spot discrepancies early, preventing errors before they manifested into larger issues.
This functionality played a pivotal role in minimizing rework throughout the project.
The Cost of Getting It Wrong
When the work involves highly specialized materials—such as orbital-welded stainless-steel piping—or regulatory approvals from agencies like the FDA, errors can lead to significant financial and operational setbacks.
For the team working on this facility, errors in the placement of MEP systems could have led to disastrous consequences.
By the time GAMMA AR was introduced, the steel structure was already in place, and the project had reached the critical phase where any misalignment in piping, drains, or outlets would result in massive rework.
Traditional 2D blueprints failed to fully capture the complexity of the project.
Errors that arose would necessitate procuring new materials, coordinating multiple trades, and risking non-compliance, failed inspections, and penalties.
Austin Parham, the project’s lead consultant, noted: “In pharma construction, if you’re able to catch a conflict early on, you will save exponential amounts of money as opposed to another industry. The magnitude is just that much greater.”
When “Good Enough” Simply Isn’t Good Enough
The hidden costs of rework go well beyond simple material replacement—they threaten the entire project timeline, budget, and compliance.
“GAMMA AR provides a level of accuracy that certainly differs from the various tools you’re using—whether it’s another technology or more traditional blueprint or floor plan reviews,” Parham noted.
With GAMMA AR, the team could not only visualize discrepancies between the model and reality but also flag issues directly on-site.
These issues are able to be synced with Autodesk Construction Cloud for fast, urgent resolution—ultimately preventing costly rework and improving communication between the field and office teams.
Missing something as simple as a drain in the wrong place could call for tearing down walls, ordering new materials, and pulling different teams away from their respective tasks to come back and fix the issue.
“In pharmaceuticals, the risks are higher because the materials are more expensive, and the systems are that much more complex,” Parham explained.
For the project team, traditional QA processes were not bringing them the results they were looking for.
On top of that, 2D plans weren’t accurately reflecting the real-world complexity of the site.
GAMMA AR Ensures Build Integrity and Compliance
Recognizing the rising potential for complications, the team turned to GAMMA AR as the project approached critical phases.
The platform’s role quickly became crucial in verifying installations before wall and ceiling closures, so that all elements were perfectly aligned and adhered to standards.
Minimizing Rework with Precision
GAMMA AR’s augmented reality capabilities allowed the team to perform a 3D-to-3D comparison between the model and the real-world installation.
This provided unparalleled results, allowing the team to visualize real-time positioning of MEP systems and move forward confidently, avoiding costly rework.
“With GAMMA AR, instead of shifting back and forth between the two worlds, you see them overlaid. This makes it seamless, especially for piping installations and visual accuracy on site,” said Parham.
“We used it to make sure everything, including outlets, drains, and data drops, was in the right spot before we closed up the walls.”
By enabling access to BIM models on-site, GAMMA AR bridged the communication gap between the field and office teams.
This integration streamlined issue tracking and ensured faster decision-making, further minimizing delays while raising project efficiency.
If these elements hadn’t been verified in time, the team would likely have been tearing out drywall and moving studs, setting the project back by days—if not weeks.
By overlaying the BIM model on the physical site, the team could verify that all elements—whether electrical outlets or data drops—were positioned correctly before closing up.
Parham emphasized this point: “GAMMA AR gives you a level of certainty in the field that’s hard to get with other tools. You can directly compare what’s in front of you with the model and know if things are accurate or not.”
Full Compliance, Right on Schedule
In pharmaceutical construction, observing regulatory standards is paramount.
GAMMA AR helped ensure compliance by validating installations before inspections and generating the documentation needed for regulatory proof.
Parham explained, “GAMMA AR allowed us to be more accurate and confident in our QA process. From a spatial standpoint, it let us verify that everything was aligned and installed correctly before we moved on to the next phase.”
From Quality Assurance to Stakeholder Engagement
Beyond improving the team’s quality assurance processes, GAMMA AR played a key role in enhancing engagement with other parties.
By enabling on-site visualization, GAMMA AR helped stakeholders understand the final look of their spaces, adding immense value by accelerating decision-making and improving communication between field and office teams.
As Parham noted, “We used GAMMA AR with some of the end users to help them visualize what their spaces would look like once completed.”
Success Beyond Expectations
With GAMMA AR, the team was able to reduce rework by over 50%, ensuring that all elements were correctly built before the walls and ceilings were closed.
As described above, the use of GAMMA AR also heightened stakeholder engagement by providing 3D visualizations and ensuring that the project stayed on track.
But the success didn’t end there.
The influence of GAMMA AR on this project was so striking that Triad Consulting Solutions immediately recognized its long-term value.
Given the high return on investment and the ability to prevent costly errors, TCS has communicated GAMMA AR’s value to their clients and will offer it as an option on future projects.
Parham notes, “We’ve seen such improvements in both time savings and cost reduction that GAMMA AR has become a tool that we offer as an option to all of our clients. It’s now something we know can be used to ensure consistency from day one.”
The Power of AR in High-Stakes Construction
This case study demonstrates how GAMMA AR is redefining precision and compliance in pharmaceutical facility construction.
By enabling on-site visualization and verification, it minimizes rework, improves decision-making, and ensures that every phase of construction meets regulatory standards with confidence.
Whether introduced later on in a project or used from the outset, GAMMA AR enhances quality assurance and fosters collaboration between stakeholders.
Its ability to catch errors before they escalate into costly delays can redefine how construction teams approach complex, highly regulated projects.
If you’re managing construction in industries where such attention to detail matters, GAMMA AR offers the solution you need to achieve accuracy, reduce risks, and stay on track.
See how GAMMA AR can minimize costly rework, ensure compliance, and streamline your project management.
Download a free trial today from the App Store or Google Play and see the difference GAMMA AR can make.
Have specific questions or want to arrange a personalized demo? Contact us today to see how GAMMA AR can meet your project’s unique needs.