Leveraging GAMMA AR for Data-Driven Jobsite Progress Tracking
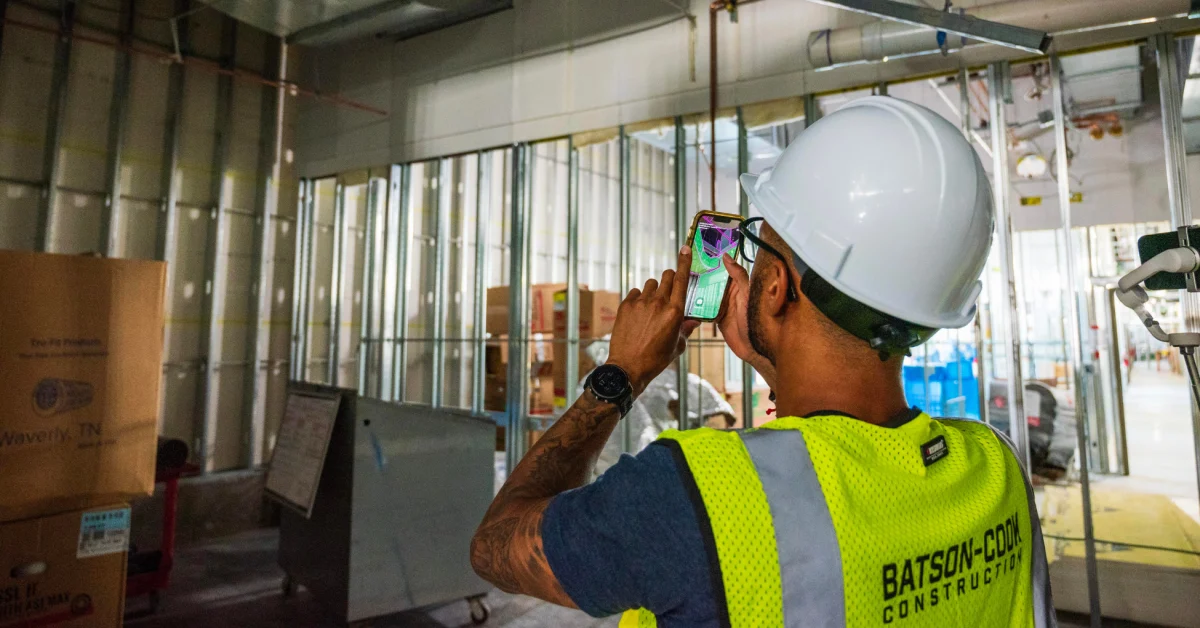
Table of Contents
Share this post
The Problem with Traditional Progress Tracking
Ask anyone in construction and they’ll tell you the painful truth—delays and cost overruns are all too common, and much of this can be traced back to inefficient progress tracking.
According to recent studies, up to 65% of construction firms report struggling with delays due to supply chain challenges alone, with poor tracking making the problem even worse.
What’s more, the hidden costs of inadequate progress tracking go far beyond time alone—they fan the flames of inefficient resource utilization, missed deadlines, and ultimately, increased project costs.
Calculating the real cost of construction delays is a complex and elusive task, because they can impact everything from labor and materials to lost revenue opportunities.
For example, in some regions, delays can account for up to 75% of cost overruns and 31% of project abandonment due to the aftershocks they send rippling throughout the project lifecycle.
Making these issues worse is having to rely on outdated tracking methods that often suffer from slow data capture with high potential for human error.
But how can construction managers gain clearer insights into their project’s progress and avoid these costly setbacks?
Project managers are focused on keeping every aspect of the construction process running like clockwork.
This involves ensuring that all moving parts—labor, materials, equipment, and timelines—stay in sync to avoid costly delays or inefficiencies.
But existing progress tracking methods often fall short in providing the kind of reliable, accurate data that project managers need to make informed decisions.
Many teams still rely on manual progress reports, where updates are collected through site walks, photos, and handwritten notes—all prone to subjectivity and human error.
While advanced technologies such as 360-degree cameras and laser scanning have become more common, they still have their own challenges.
360-degree cameras provide a visual snapshot of the jobsite but demand considerable post-processing to extract actionable data.
Similarly, laser scanning can bring precise measurements, but the technology can be costly, time-consuming, and requires its own kind of specialized expertise.
Both methods can slow down the pace of decision-making, as the time taken to process the data delays the feedback loop that project managers depend on.
As a result, these tracking methods can still leave room for guesswork, leading to misaligned expectations, underutilized resources, and preventable rework.
The lack of seamless, regularly updated data often means that by the time an issue is detected, it has already impacted the project timeline or budget.
This creates a gap between what’s happening on-site and the project management’s ability to respond effectively, raising the chances of delays and cost overruns.
Progress Tracking Pitfalls: The High Cost of Misalignments
Poor data capture and communication on construction sites create a kind of domino effect, leading to costly errors and delays.
Discrepancies between planned schedules and actual on-site progress are a frequent source of delays, often resulting in missed milestones if not identified early.
If not caught soon enough, even small misalignments can mushroom into delays that inflate project costs by 10-20%.
For superintendents and project managers, not having reliable, up-to-date project data can lead to reactive (always putting out fires) rather than proactive management.
Inaccurate or outdated information not only heightens the chances of expensive rework but also complicates resource management, including coordinating subcontractors, materials, and labor.
Progress tracking is also closely linked to payouts, and when transparency is weak, this can lead to delays in payments, disputes, and strained relationships with subcontractors and suppliers, further impacting the project’s timeline and budget.
Even when discrepancies do get detected, the process used for reporting and resolving them is often inefficient, further stretching out project timelines.
Optimized Progress Tracking with GAMMA AR
While traditional progress tracking tools alone may fall short, leveraging GAMMA AR helps bridge the gap between planned designs and real-world site conditions.
Here’s how it works: using GAMMA AR, superintendents and foremen can overlay 3D virtual models onto the physical environment via their mobile devices, allowing them to see where as-built conditions align or diverge from the original BIM models.
With this overlay, they can also track the construction status of building parts, components, and elements in real time, marking them as completed to ensure progress is well documented.
GAMMA AR captures and shares site-specific data, including photos and notes, all linked to BIM elements and accessible as a single source of truth for both onsite and offsite teams.
This flow of information empowers construction managers to make more informed, timely decisions based on the most up-to-date data available.
Next-Gen Progress Tracking for Today's Jobsite
Whether in the field or the office, teams have access to the same up-to-date information on how the in-progress construction aligns with schedules.
This drastically improves collaboration and communication.
By empowering construction managers with the latest visual data, GAMMA AR significantly enhances issue reporting and resolution.
In one residential project, GAMMA AR provided immediate insights into construction progress, helping identify potential misalignments with the schedule and nearly 100 instances that could have led to significant cost overruns if not addressed early.
By resolving these issues early on, the project avoided substantial delays and rework.
Supporting Existing Progress Tracking Workflows
With GAMMA AR, construction managers can visually compare the BIM models against the job site, allowing them to visually compare planned progress with actual conditions.
By marking the status of building components directly within the model, they can track completions, anticipate delays, and allocate resources more efficiently to keep the project on schedule.
Progress data collected via traditional methods can be further enhanced using GAMMA AR, verifying the accuracy of what’s been reported.
With both quantitative and qualitative insights in hand, construction managers gain a clearer understanding of progress during reviews.
GAMMA AR’s advanced visualization tools make it easier to spot potential delays and ensure issues are addressed promptly.
The ability to visualize discrepancies on-site tightens the feedback loop, preventing issues from slipping through the cracks and leading to faster resolution with minimal back-and-forth between stakeholders.
The Future of Data-Driven Progress Tracking
As construction projects grow more complex, AR technology like GAMMA AR will become essential for data-driven management.
The ability to visualize and analyze real-time site conditions in relation to BIM models will enable teams to stay ahead of potential issues and optimize project outcomes.
By integrating GAMMA AR, construction teams can future-proof their operations, paving the way to better outcomes and safeguarding their hard-won margins.
Elevate Your Progress Tracking (and more!) with GAMMA AR
Discover how this tool can improve efficiency, reduce delays, and optimize your project outcomes.
Download the fully functional free trial today from the App Store or Google Play, and if you’d like a personalized demo or have any questions, feel free to reach out to our team for support.