Foresight is better than hindsight
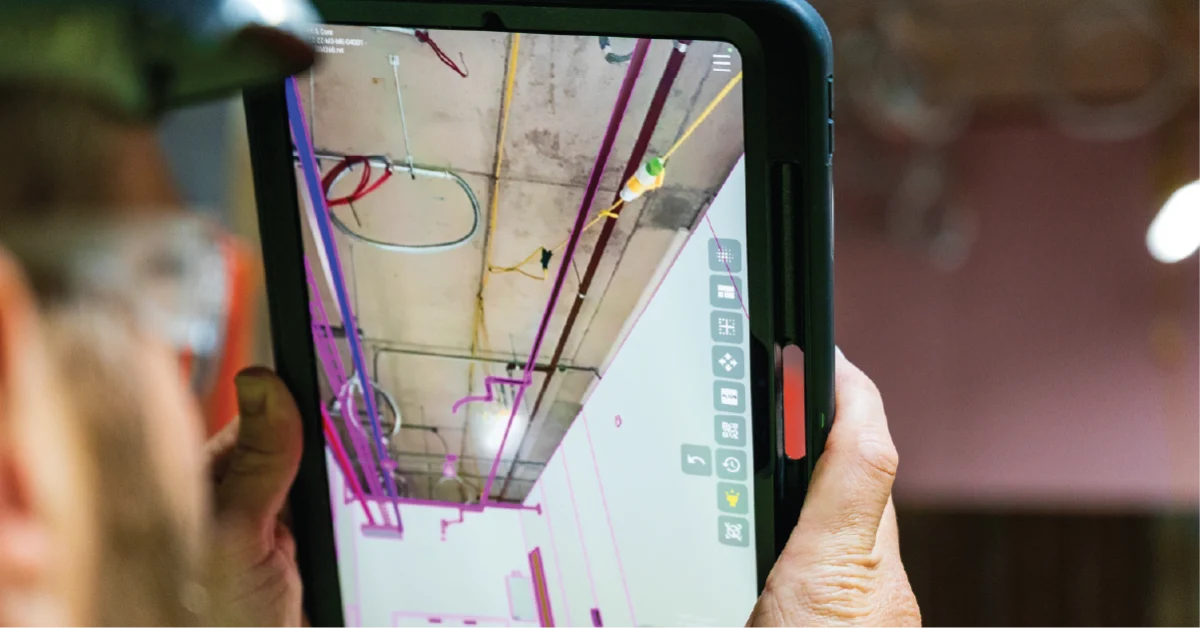
Table of Contents
Share this post
Why most job sites perform QA/QC too late: A case for preventative action
Today, all on-site methods for performing QA/QC in construction projects have something in common: focusing on the past and trying to handle what went wrong rather than ensuring correct execution.
A combination of many factors leads to errors and rework, resulting in 4-10% of construction costs. A heavy burden on the construction industry, which is plagued by labor shortages (especially of experienced labor), increased material prices, as well as an ever-increasing project complexity and heightened project requirements.
Except for experienced field professionals, which are declining in numbers, not much stands in the way of deviations and mistakes manifesting on-site. The tools which are commonly used on sites today, such as scanning solutions, do not catch problems before they happen and are not well suited for preventing rework or delays from arising in the first place. They simply are showing the past.
What is really needed to improve decision making on site is a look into the future. Today, augmented reality provides us with the technology to see the past of a construction site together with the future.
Foreseeing the future
This visual combination of the existing (past) and the future of the construction project provides field teams the foresight required to impactfully preempt or resolve issues arising in construction. The overlay of the 3D/BIM models onto the actual site creates clarity over the correct way of execution and helps to coordinate disciplines through unambiguous communication. The positive impacts on rework and construction schedules scale with the complexity of the projects. The effects become very evident especially with highly installed projects where 2D drawings simply fail to deliver intuitively understandable information easily.
In addition to execution problems, design flaws also need to be addressed. The decision-making and knowledge required for their prevention and resolution require great foresight, which is typically linked to highly experienced individuals. Even with their support, too many flaws end up being built, only to be reworked soon after. Too many potential optimizations are missed out, as they are not “seen” early enough.
And as most projects today perform concurrent planning activities during the construction phase, there is a definite need for continues, real-time checking of potential issues on site.
This way, field teams “foresee” the potential consequences of executing the current plan, while comparing 3D/BIM models to actual on-site conditions in real time. Thus, improving informed decision making directly on site to avoid issues from arising and initiating well defined RFI requests directly on site.
Using AR construction companies can perform QA/QC on site before and during construction works as a preventative measure that increases the performance of the overall project ensuring heightened quality while reducing the chances of unplanned circumstances.
The measurable success of AR implementation
The results speak for themselves. Companies such as TCS , a Georgia, USA-based construction management company specializing in pharmaceutical facilities and other process-heavy projects, reported rework savings of 50%through enhanced collaboration between field and office teams through on-site issue tracking and visualization and improved stakeholder engagement for faster decision-making and project alignment. One of Germany’s leading GCs – Goldbeck, states time savings of 80% for on-site QA/QC processes and 79% of faster detection of clashes on site.
This is why we have built GAMMA AR: to act as a focal point for intuitive information exchange, improving clarity and understanding directly on the construction site.
So that the people we work with can steer projects better and take better preemptive decisions, ensuring correct execution while facilitating issue-resolving action early on in the construction process.